Sizing and selecting precision gear pumps for specific applications involve a systematic process to ensure that the pump chosen meets the requirements of the application.
Here are the steps and considerations for sizing and selecting precision gear pumps:
- Understand Application Requirements:
- Start by thoroughly understanding the specific requirements of your application. Identify the desired flow rate, pressure, and fluid properties. Consider factors like viscosity, temperature, and the type of fluid being handled.
- Define System Characteristics:
- Determine the characteristics of the overall fluid system, including the piping, tubing, valves, and other components. This will help you understand the resistance or head pressure the pump needs to overcome.
- Select the Right Material:
- Choose materials for the pump and its components that are compatible with the fluid being pumped. Consider factors like chemical resistance and wear resistance.
- Calculate Flow Rate:
- Calculate the required flow rate (Q) based on your application’s needs. Ensure that the pump can provide the necessary flow while accounting for safety margins.
- Determine Pressure Requirements:
- Establish the required pressure (P) that the pump must generate to overcome system resistance. Consider the dynamic head, frictional losses, and the highest point of elevation in the system.
- Consider Operating Conditions:
- Evaluate the operating conditions, such as temperature ranges, to ensure that the selected pump can handle the specific environment. For applications with extreme temperatures, choose a pump designed for those conditions.
- Factor in Viscosity:
- Account for the viscosity of the fluid, which can significantly affect the performance of precision gear pumps. High-viscosity fluids may require specific pump designs or larger clearances.
- Estimate Horsepower Requirements:
- Calculate the required horsepower based on the flow rate and pressure. Ensure that the selected pump motor can provide the necessary power.
- Evaluate Pump Speed:
- Determine the pump’s speed, typically measured in revolutions per minute (RPM), to achieve the desired flow rate. Ensure that the pump is capable of operating at the required speed.
- Consider Pump Design:
- Evaluate the design features of precision gear pumps, such as gear type (spur or helical), clearances, and the number of stages. Choose a pump design that aligns with the application’s requirements.
- Review Efficiency:
- Examine the volumetric efficiency of the pump. Higher efficiency pumps will minimize energy consumption and offer better performance.
- Check NPSH (Net Positive Suction Head):
- Verify that the available NPSH in your system exceeds the NPSH required by the pump to prevent cavitation.
- Safety and Compliance:
- Ensure that the selected pump complies with safety and industry standards relevant to your application. This is particularly important in industries like food and pharmaceuticals.
- Maintenance and Service:
- Consider the ease of maintenance and availability of service and replacement parts for the selected pump. This will help ensure long-term reliability.
- Consult with Experts:
- If you’re uncertain about the pump selection, consider consulting with experts or the pump manufacturer. They can provide valuable insights and recommendations based on their experience.
- Compare Options:
- Compare different precision gear pump models and brands to find the one that best meets your application’s requirements while considering factors like cost, lead time, and warranty.
- Perform Testing:
- When possible, conduct real-world testing of the selected pump in your specific application to validate its performance.
By systematically following these steps and considering all relevant factors, you can size and select the most suitable precision gear pump for your specific application, ensuring that it meets your flow rate and pressure requirements while maintaining efficiency and reliability.
What are the advantages and limitations of precision gear pumps compared to other pump types?
Precision gear pumps offer several advantages for specific applications, but they also have some limitations compared to other pump types. China Precision Gear Pumps Understanding these pros and cons will help in making informed decisions about pump selection.
Here’s a summary of the advantages and limitations of precision gear pumps:
Advantages of Precision Gear Pumps:
- High Precision and Accuracy: Precision gear pumps are renowned for their ability to provide highly precise and accurate flow rates, making them suitable for applications requiring consistent and controlled fluid delivery.
- Low Pulsation: They generate minimal pulsation, resulting in a smooth and continuous flow, which is crucial in applications sensitive to flow variations.
- Efficiency: Precision gear pumps offer high volumetric efficiency, maximizing fluid transfer while minimizing energy consumption.
- Compact Design: They are often compact and space-efficient, making them suitable for applications with limited installation space.
- Viscosity Handling: These pumps can handle a wide range of fluid viscosities, from low to high, without significant loss of performance.
- Low Shear: Precision gear pumps are gentle on shear-sensitive materials, making them suitable for applications involving delicate substances like biological samples.
- Metering and Dosing: They excel in metering, dosing, and dispensing applications, where accurate control of fluid quantities is essential.
- Material Compatibility: Precision gear pumps can be constructed using materials compatible with a wide range of fluids, including corrosive and abrasive substances.
- Sanitary and Aseptic Applications: They are suitable for sanitary and aseptic applications in the food and pharmaceutical industries due to their cleanability and sterilizability.
Limitations of Precision Gear Pumps:
- Low Flow Rates: Precision gear pumps may not be ideal for applications requiring extremely high flow rates. They are typically better suited for low to medium flow applications.
- High Viscosity Limitation: Handling very high-viscosity fluids may require specialized precision gear pump designs or modifications.
- Limited Solids Handling: These pumps are generally not designed for handling solids, and the presence of solid particles can lead to wear and reduced efficiency.
- Complex Lubrication: Some precision gear pumps require specialized lubrication systems, adding complexity to maintenance.
- Wear and Tear: Like all mechanical components, precision gear pumps can experience wear and may require regular maintenance and replacement of components.
- Higher Costs: Precision gear pumps, especially those designed for highly precise applications, can be more expensive than some other pump types.
- Limited Pressure Capabilities: While precision gear pumps can handle moderate to high pressures, they may not be suitable for extremely high-pressure applications.
- Sensitive to System Changes: Precision gear pumps can be sensitive to changes in system conditions, such as variations in backpressure or fluid properties.
- Complexity in Design: Achieving the high precision of gear pumps can involve intricate design and manufacturing processes, which may result in a higher level of complexity compared to some other pump types.
The choice of pump type should consider the specific requirements and limitations of the application. While precision gear pumps are excellent for many applications, including those that demand high precision and low pulsation, they may not be the best choice in situations where other pump types may be more suited to the task.
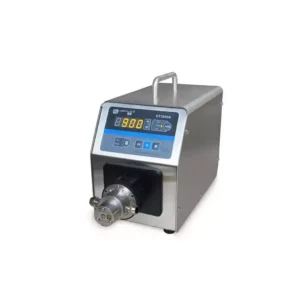